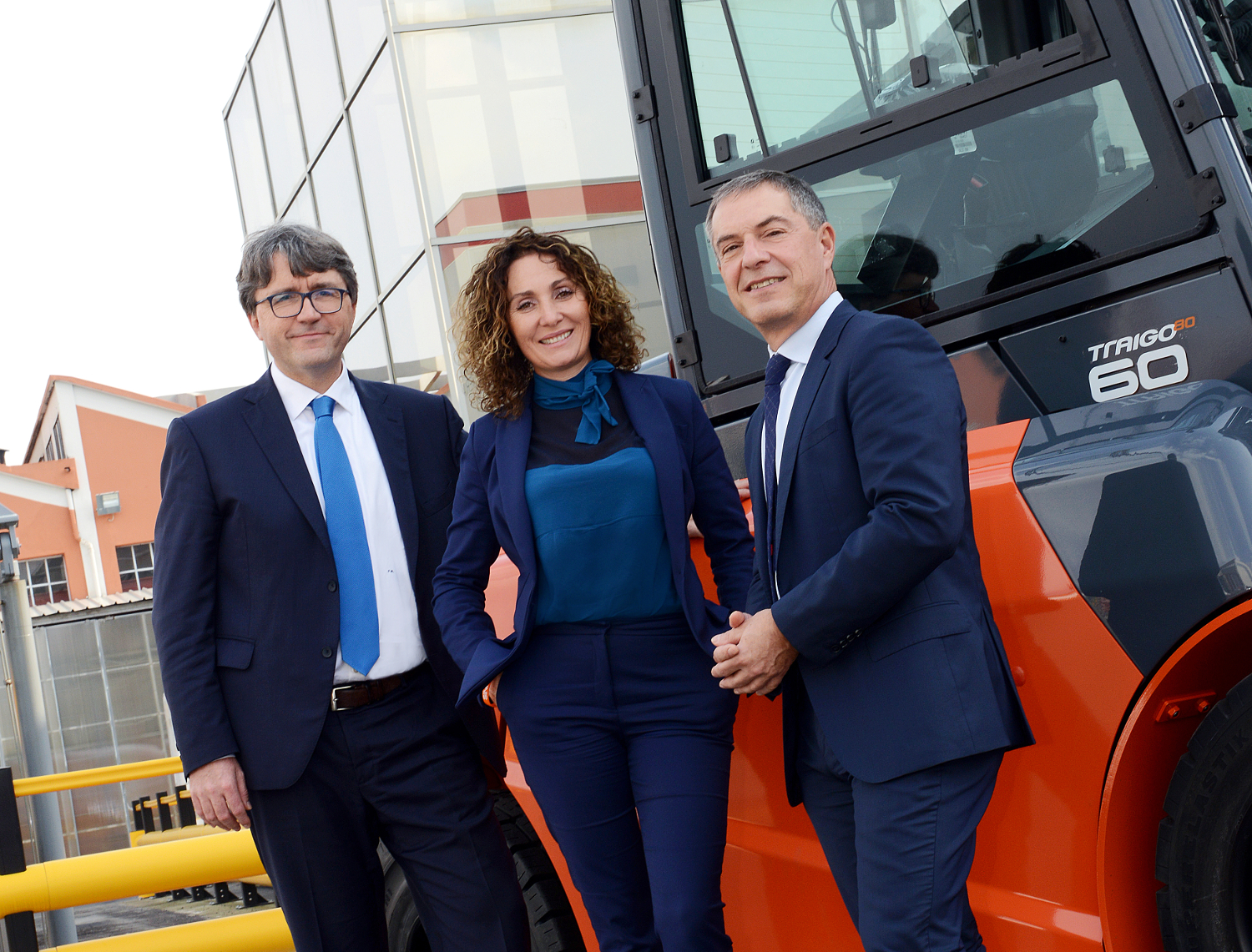
Il piano di trasformazione digitale della storica fabbrica di carrelli elevatori, acquisita dal colosso giapponese nel 2000, ha richiesto la completa riscrittura della piattaforma ERP/MRP per una produttività e una qualità ancora più spinte. E uno stile italiano ammirato da tutta Toyota Industries Corporation
Ancora una volta, il racconto della trasformazione digitale resa possibile dalle tecnologie e dal know-how firmati Sinfo One, ci porta non troppo lontano dal quartier generale della società di software e consulenza parmense. Restiamo in Emilia, anche se dentro a una sorta di enclave giapponese, incastonata nella periferia industriale di Bologna, dove il gruppo Toyota non costruisce automobili ma sofisticati carrelli elevatori, altrimenti conosciuti come “muletti” o “smart trucks”, commercializzati in tutto il mondo con il brand Toyota.
Rispetto agli incontri precedenti, una differenza c’è, e non di poco conto. Finora su Data Manager, Sinfo One era sempre stata protagonista dell’information technology al servizio dell’industria di trattamento alimentare e dell’agricoltura 2.0. Oggi, la ritroviamo al centro di un ambizioso progetto di trasformazione nella gestione dei processi di una fabbrica appartenente a un colosso che ha conquistato una reputazione quasi leggendaria proprio per le sue rivoluzionarie metodologie per il controllo della produzione manifatturiera. Un progetto di respiro globale che restituisce un’immagine più completa della software house guidata da Paola Pomi nel suo ruolo di amministratore delegato, che proprio quest’anno ha sancito il definitivo passaggio generazionale nel management della società fondata dal padre. Sinfo One genera ormai un’importante quota del suo fatturato – circa il 30% dichiara con orgoglio l’AD Pomi – con clienti esteri. Il suo percorso di internazionalizzazione riguarda anche la sfera finanziaria, con l’ingresso, un anno fa, nella compagine azionaria di due soci di peso come il gruppo alimentare tedesco Tönnies (leader europeo nel trattamento delle carni) e il private equity di Fondo Agricolo Italiano I (FAI I), di proprietà della francese Unigrains, storica holding di investimento specializzata nell’agri-food e nella ricerca di tecnologie per il food che rappresenta oltre 150 coltivatori di cereali.
BISOGNO DI ARMONIZZAZIONE
La collaborazione con Toyota Material Handling Manufacturing Italy nasce quasi contemporaneamente ad un’altra partnership di Sinfo One. Dal 2016, infatti, l’azienda di Parma fa parte di Redfaire International, la joint venture che riunisce le maggiori società di consulenza mondiali specializzate sulla piattaforma ERP Oracle JD Edwards Enterprise One. Toyota Material Handling Manufacturing Italy ha coinvolto gli esperti di Sinfo One in un progetto che secondo Giorgio Polonio, amministratore delegato di Toyota Material Handling Manufacturing Italy, viene monitorato con grande interesse dal top management del grande gruppo nipponico, impegnato a portare avanti la sua ambiziosa strategia di digital transformation. «Tutto parte tre anni fa – racconta Paola Pomi – quando TMHMI commissiona un approfondito assessment dell’ambiente ERP destinato a rimpiazzare un precedente mosaico di soluzioni che appariva sempre meno adeguato alla flessibilità richiesta oggi, soprattutto dal punto di vista dell’armonizzazione all’interno del Toyota Production System». L’ambiente software utilizzato fino a quel momento – continua l’AD di Sinfo One – «mostrava i segni delle cicatrici lasciate dai diversi interventi avvenuti nel corso del tempo. Proprio come avviene per la nostra pelle, le cicatrici riducono l’elasticità».
LA SCELTA DI RINNOVAMENTO
Ma com’è maturata la scelta di rinnovamento basato su JD Edwards? L’AD di TMHMI ci aiuta a ripercorrere le tappe principali di una storia di impresa simbolo del saper fare italiano. La fabbrica che oggi fa parte di uno dei marchi più affermati del settore automotive, viene fondata nel 1942 e inserita tra le attività del gruppo industriale sviluppato a partire dal primo dopoguerra da una importante famiglia bolognese. La vecchia CESAB è stata per sessant’anni uno dei maggiori produttori di carrelli elevatori italiani, autonomo fino all’anno 2000, quando la tipologia di carrelli prodotti – del tipo a “controbilanciamento”, tipicamente utilizzati negli esterni degli ambienti industriali – suscitò l’interesse della svedese BT Industries, specializzata nella produzione dei carrelli retrattili, quelli più utilizzati all’interno degli spazi di lavoro, ritenuti complementari.
Al momento di quella acquisizione, BT era già entrata nella sfera di interesse di Toyota in Europa. E così pochi mesi dopo, la fabbrica italiana si ritrova a far parte, insieme ad analoghi siti produttivi in Svezia e Francia, del braccio europeo di TICO, Toyota Industries Corporation. A sua volta, la vocazione industriale di questa sussidiaria di Toyota Group si rifà alle origini storiche di una conglomerata nata più di 90 anni fa, non per costruire automobili ma per fornire telai meccanici, la moderna industria del tessile.
«In breve tempo quella che era un’importante realtà italiana, in grado di produrre in un anno tremila carrelli elevatori, assume il marchio Toyota, che nella sola Europa conta 10.600 dipendenti, un terzo dei quali impegnati in aree produttive».
Un contesto in definitiva completamente diverso, a partire dall’output generato: quasi sei volte superiore a quello raggiunto da CESAB al culmine della sua storia. Una parte importante del percorso di cambiamento che ha portato alla collaborazione con Sinfo One riguarda certamente l’approccio alle tecnologie. Il primo referente di Paola Pomi è Patrick Malservisi, IS/IT director di Toyota Material Handling Europe Supply. «A livello corporate – spiega Malservisi – in Toyota esiste una funzione IT centralizzata che attraverso un CIO di gruppo esprime le linee strategiche in materia informatica. Sui siti produttivi, i processi più legati alla fabbrica e alla ricerca e sviluppo sono governati da responsabili IS/IT». Due funzioni – prosegue Malservisi – che oggi hanno molti elementi condivisi ma che mantengono specificità proprie, soprattutto negli aspetti applicativi riguardanti le singole produzioni. «Un altro punto di congiunzione – ricorda Polonio – è proprio il Toyota Production System, che rappresenta una leva di sviluppo dentro e fuori dalla fabbrica nel miglioramento continuo del servizio al cliente. Nel grande contenitore del servizio da erogare a contorno del prodotto fisico, occorre riversare tanto contenuto tecnologico, che si concretizza nell’infrastruttura sviluppata a sostegno della strategia».
Polonio e Malservisi insistono molto su questo spostamento di baricentro da una filosofia di vendita basata sulla qualità del prodotto a una strategia che deve curare la qualità del servizio al cliente e più in generale dell’esperienza che quest’ultimo deve sperimentare.
«Se in passato la qualità del prodotto bastava come motivazione all’acquisto, oggi il servizio post-vendita e in misura crescente la user experience diventano una formidabile leva decisionale per i nostri clienti. E la funzione IS/IT pesa tanto perché servizio ed esperienza sono fatte di molti elementi puramente soft».
IL FUTURO È DIGITALE
Nel momento di rilevare la società svedese che aveva da poco acquisito CESAB, Toyota Material Handling è già presente in Europa con uno stabilimento a Nantes, ma è a Bologna che la cultura di fabbrica giapponese trova molta sintonia e un immediato gioco di sponda. Gli italiani – racconta Polonio – hanno imparato molto dalla cultura del Toyota Production System (TPS). «Si è trattato di un passaggio non facile, quello da una cultura dei prodotti “a stock”, alla filosofia del “make to order”, con le linee di produzione a “flusso teso”, nessun magazzino, nessuno spazio in cui depositare le componenti che i fornitori consegnano letteralmente nel momento in cui servono per la fabbricazione». In questa fase di transizione, i 300 fornitori di CESAB si riducono a 160, molti dei quali arrivati con la nuova gestione dell’impianto. Sono tutti dettagli importanti per capire la storia di trasformazione realizzata oggi con Sinfo One, così come è importante rilevare il felice connubio che giapponesi e italiani hanno saputo costruire sulle rispettive doti di organizzazione e creatività. Nei quasi due decenni trascorsi dal 2000, vengono avviate due fasi di “sviluppo congiunto”. Da entrambe usciranno modelli di carrelli controbilanciati molto apprezzati dai clienti. Dopo 20 anni, alla fine di un ciclo che vede TMHMI ormai attestata su una produzione annua di 17mila carrelli, con il pieno dominio del TPS in tutte le sue sfaccettature, l’azienda ha dovuto inevitabilmente concentrarsi sulla revisione dei suoi processi in chiave di trasformazione digitale. «Un termine forse abusato – riconosce Polonio – ma che rende bene l’immagine di una filiale europea che da questo punto di vista, non trova nella casa madre giapponese un valido benchmark».
Ma come si spiega questo apparente paradosso? Nel settore auto, Toyota è il produttore globale numero uno, e il merito va sicuramente alla sua efficienza produttiva. Il Toyota Production System sembra più inesorabile di un algoritmo digitale. «Può sembrare strano» – riconosce Patrick Malservisi. «Non dimentichiamo però che il TPS riguarda la fabbrica, non il lavoro d’ufficio. L’idea è che bisogna andare sì verso la smart factory, ma anche verso lo smart work». Inoltre – prosegue Malservisi – «bisogna considerare che il successo del TPS, un algoritmo pensato per le persone, è legato alla maniacale precisione con cui i processi vengono pianificati e seguiti da decisori ed esecutori umani. In Europa e prima ancora negli Stati Uniti, i sistemi di produzione trovano un crescente supporto nella digitalizzazione ed è naturale che la casa madre presti grande attenzione alle dinamiche di cambiamento dei sistemi informativi e dei processi nelle sue realtà internazionali». E forse non è un caso, se il Digital Technology Research Forum – nato per volontà dell’intero gruppo TICO per studiare e definire le linee guida di una efficace trasformazione digitale – ha tenuto la sua prima riunione pochi mesi fa proprio a Bologna, dove si sono riuniti i responsabili IS/IT dei siti di Toyota Material Handling Manufacturing e di altre realtà.
UN CARRELLO PIENO DI SERVIZI
«La parola chiave è crescita» – interviene Polonio. La divisione Motors di Toyota ha avuto una espansione organica, ogni volta esportando in geografie diverse i suoi modelli produttivi, mentre la parte di veicoli e attrezzature industriali di TICO si è evoluta per acquisizioni successive, generando al suo interno una certa disomogeneità di sistemi informativi. «In Italia, siamo stati a suo tempo pionieri di una prima fase di ridisegno infrastrutturale dell’azienda, ma alla fine ci siamo limitati ad aggregare, su ambiente AS400, una serie di applicativi giudicati più rilevanti». Questa situazione ha resistito sostanzialmente immutata fino a quando, all’inizio del 2017, la pressione sui sistemi informativi non ha raggiunto il livello di guardia. Le nuove esigenze della “servitizzazione” che accompagnano i prodotti fisici generano una spinta verso una maggiore uniformità.
«Qualità del prodotto, del servizio e dell’esperienza richiedono una maggiore integrazione e condivisione delle informazioni. E uno degli strumenti da applicare è la business process harmonization».
Quella che oggi è a livello corporate una missione operativa su scala globale, nei siti produttivi Toyota corrisponde a un percorso avviato da tempo. «Una maggiore armonizzazione dei nostri sistemi informatici – precisa Malservisi – ci permette di lavorare meglio in direzione degli obiettivi di servizio. La digitalizzazione può essere una bella leva per introdurre novità come l’Agile e altri tipi di approccio». Tutta una serie di obiettivi, impossibili da perseguire con i sistemi legacy di Bologna.
Il progetto di trasformazione è partito da una “short list” di soluzioni che includeva due piattaforme ERP. La scelta è ricaduta sulla suite Oracle JD Edwards EnterpriseOne, il cui modulo MRP (Material requirements planning) risulta particolarmente allineato agli obiettivi di TMHMI. La stessa soluzione è stata adottata anche da Toyota Material Handling Manufacturing Sweden, attraverso un processo di selezione indipendente. Anche gli americani di Cascade, un’altra azienda Toyota che produce accessori per carrelli elevatori, si sono orientati verso lo stesso software. Criteri altrettanto rigorosi hanno guidato TMHMI nella scelta del partner di progetto.
«In Sinfo One abbiamo visto un’azienda che condivide un approccio al business molto simile al nostro. Una società finanziariamente solida, familiare ma con una cultura aziendale da public company, con un importante numero di dipendenti e un’ottima reputazione». Sinfo One ha dovuto seguire la stessa procedura di certificazione che Toyota applica ai suoi fornitori per ambire al ruolo di partner.
«Alla fine, abbiamo certificato l’esistenza di tutti i requisiti del caso. Inclusa l’affiliazione con il consorzio internazionale di consulenti Oracle JD Edwards che ha seguito altri progetti di TICO a livello internazionale (sempre in modo indipendente)».
UN NUOVO MODO DI LAVORARE
L’approfondito assessment dell’ambiente ERP: ha inizio così quello che per Paola Pomi è stato un periodo di “fidanzamento”. «In questa fase, abbiamo analizzato, tutti insieme e in ogni dettaglio, i processi di produzione Toyota inseriti nel sistema informativo legacy» – traduce l’AD di Sinfo One. Fase alla quale ha fatto seguito il “matrimonio” vero e proprio: il progetto del futuro sistema di supporto alla produzione, concepito non come un banale copia e incolla delle procedure codificate in passato, ma come lo schema di un nuovo modo di lavorare in armonia con il TPS. Un obiettivo per niente banale per una riscrittura che si era posta il vincolo di sfruttare il più possibile le funzionalità standard di JD Edwards EnterpriseOne, per ottimizzare tempistiche, costi e gestione dei rischi. «Dove non era possibile rimanere nel solco dello standard che avevamo approfonditamente studiato, abbiamo sempre cercato di implementare una soluzione che fosse davvero in grado di garantire un effetto leva sul nostro lavoro quotidiano, supportandoci in un modo orientato al nostro futuro» – dichiara Malservisi. Sotto le indicazioni del comitato direttivo del progetto, i professionisti di Sinfo One sono intervenuti sulle modalità di interazione con i fornitori, sul livello prestazionale del sistema MRP, reso ancora più potente e completo. Le personalizzazioni hanno aggiunto persino funzionalità di manufacturing enterprise planning senza dover acquisire specifici moduli alla piattaforma.
L’aspetto di cui Paola Pomi e il suo cliente vanno particolarmente orgogliosi è la naturalezza e l’efficacia con cui il sistema MRP di TMHMI è stato plasmato in base alle peculiari esigenze della messaggistica KANBAN e Junjo che regola il delicato meccanismo delle forniture che arrivano dall’esterno direttamente sulle linee di assemblaggio. La linea produttiva, che i giapponesi di Toyota hanno tracciato come nell’ottica della “fabbrica in continuo miglioramento”, funziona a flusso teso. Non ci sono momenti di sosta dedicati all’approvvigionamento dei pezzi da assemblare, né spazi di attesa dove concentrare questi pezzi. Tutto deve funzionare in modo fluido, previa accurata pianificazione dei prodotti da assemblare e i fornitori, che devono essere a conoscenza di questi piani e che ricevono anche più volte in una stessa giornata l’avviso con la richiesta dei pezzi che dovranno essere disponibili al momento opportuno, in quel dato ordine per un determinato punto della linea. Precisando meglio il concetto, Giorgio Polonio spiega che il TPS non prescrive che il magazzino lo faccia il fornitore:
«Anche i singoli pezzi dei fornitori vengono prodotti secondo un analogo principio just in time. In un contesto del genere, si deve necessariamente puntare a una drastica riduzione dei margini di errore, perché ogni piccolo intoppo può propagarsi, a cascata, coinvolgendo intere linee produttive».
L’impatto della nuova piattaforma implementata da Toyota va anche in direzione di una pianificazione più intelligente e automatica e di una produzione capace di adattarsi meglio agli errori commessi. «Abbiamo già avuto risultati tangibili in questo senso, con una riduzione delle persone impegnate nella pianificazione giornaliera» – spiega l’AD di TMHMI. «Naturalmente, l’obiettivo è riutilizzare queste risorse per incarichi a maggior valore aggiunto». Meno persone, meno documenti cartacei, processi ottimizzati, maggiore resilienza in caso di errore: in pratica, il mantra della trasformazione digitale.
ACCELERARE IL CAMBIAMENTO
Ancora più sorprendente è la modalità attuativa con cui Toyota Material Handling Manufacturing ha realizzato tutto questo. Nelle fasi culminanti, il progetto ha coinvolto una ventina di esperti di Sinfo One e circa quaranta “key user” della realtà bolognese. In media, nelle varie fasi di implementazione, hanno lavorato 20 massimo 25 key user. Per il go-live è stata scelta la formula del “big bang”: nella data prevista per il lancio, il vecchio sistema è stato spento e JD Edwards Enterprise One è stato acceso. Oggi, delle 570 persone che lavorano per TMHMI circa un terzo – tra white collars e personale tecnico – ha accesso al nuovo ERP.
Malservisi si sofferma a lungo sull’aspetto della user experience, sul clima positivo che si è venuto a creare durante il progetto, sul coinvolgimento, la curiosità espressa da tutti. «I primi utenti sono diventati i veri evangelizzatori della soluzione» – racconta il capo del progetto. «I colleghi fanno domande e loro rispondono. In tutti, c’è una grande curiosità e tanta voglia di aggiungere funzioni nuove. L’altro giorno, un giovane collega mi ha detto: Patrick, adesso ho una Ferrari in garage, voglio poterla guidare bene. Ma abitando a Maranello, l’ho perdonato per aver menzionato il nome di un concorrente».
La soddisfazione è leggibile nello sguardo di Paola Pomi, che commenta: «Tutta l’operazione Toyota è un’ulteriore prova del positivo riconoscimento delle implementazioni di Sinfo One per conto di clienti all’estero. Il nostro brand continua a essere percepito positivamente come esempio di imprenditoria familiare italiana, ma la presenza di due stakeholder internazionali ci ha conferito una statura che in passato ci mancava». Un tassello prestigioso, prezioso dal punto di vista del marketing. Ma c’è anche una forte componente di valore intrinseco. Il fondo di private equity, formalmente italiano ma di origine francese, è una potente interfaccia verso un intero mondo di imprese dell’industria alimentare, un orecchio sensibile alle richieste di un mercato con un fabbisogno sempre più forte di prodotti e soluzioni. Con lo stesso gruppo Tönnies, Sinfo One sta studiando nuove estensioni ai gestionali finora implementati, nuove applicazioni capaci di andare oltre gli aspetti della gestione quotidiana, della business intelligence e della pianificazione. «Pensiamo al tema della qualità del prodotto, con la progressiva automazione dei sistemi di controllo avanzato» – continua Paola Pomi. «Ma anche all’impiego del machine learning e dell’intelligenza artificiale nella ricerca di nuove tendenze di consumo per i prodotti alimentari, caratterizzati da forti variazioni di stagionalità e di gusto del pubblico».
OLTRE LE PIATTAFORME ERP
Grazie al successo delle sue implementazioni, Sinfo One anche quest’anno ha chiuso il suo anno di esercizio al 31 ottobre, superando l’EBITDA prefissato.
«È un traguardo notevole perché gli obiettivi che ci eravamo dati, anche in relazione alle aspettative dei nuovi soci, erano particolarmente sfidanti»
– afferma Paola Pomi, sottolineando che il risultato si spiega con la bravura di tutti i 155 dipendenti della società e degli altri collaboratori, ma anche grazie all’azione che Sinfo One riesce a svolgere in comparti tecnologici e su applicazioni che prima non potevano essere affrontati con la stessa efficacia. In particolare, l’AI è uno di questi argomenti. «Stiamo inoltre presidiando il tema della blockchain, su alcune specifiche esigenze non solo estese alla filiera della supply chain, ma anche su tematiche riguardanti per esempio la certificazione dei contratti di fornitura. Con l’aiuto di clienti interessati, stiamo sperimentando nuove metodologie di implementazione, mescolando aspetti tipici della blockchain con altri mutuati dalla nostra esperienza in campo ERP, scalando le soluzioni per renderle interessanti anche per aziende di piccole e medie dimensioni».
La sperimentazione avviene anche su frontiere avanzate come la robotic process automation, l’uso di robot software per emulare quelle forme di interazione tra essere umano e sistema digitale, rendendo automatica la gestione di un determinato processo di business.
«Sono già 4 i clienti live con progetti di Robotic Process Automation, sia di piccole che di grandi dimensioni, e questo è per noi un grande vanto»
dichiara Paola Pomi senza falsa modestia. Sinfo One applica metodologie e tecnologie innovative, finora inesplorate, in un’ottica di accelerazione e semplificazione, per far sì che le classiche piattaforme ERP diventino uno strumento sempre più autonomo, utile, e duttile, nelle mani dei loro utenti finali.
Foto di Gabriele Sandrini